Casting is a process used to manufacture a
product or unfinished product by shaping the raw material. Vacuum casting is a type
of casting process which is mostly used to produce some plastic parts, during
this process the material is held in a vacuumed casting cabinet that cabinet
then placed over the pattern to make the desired shape, lastly the material is
filled in the casting cabinet.
Vacuum casting process is being used globally
as it is less time consuming and delivers quick results. It has a thin layer of
plastic with some lubricity that helps in getting the product quickly.
Additionally, there are no chances of defects due to moisture, no need of
binders, and it doesn’t produce a toxic fume that’s why it is a popular and
amazingly great casting technique.
When using any other time taking casting
method, an industry has to collect the material way prior to start the
manufacturing process, which at times gets wasted due to non-usage. Whereas
vacuum casting is a quick manufacturing process that requires the material only
once the production stage is about to start. This is also a big reason why
manufacturing industry prefers this method.
This casting method is generally used to
create rubber or plastic components and parts which are precise and
dimensionally accurate. The process consists of the steps that are mentioned
below.
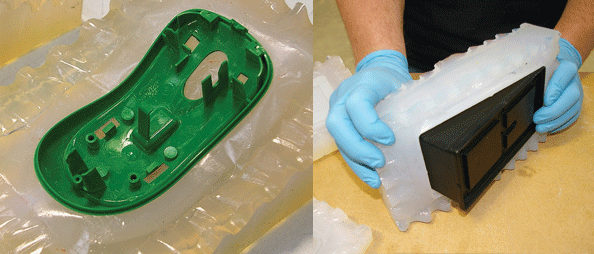
First things first, a 3D CAD data is used to create the master pattern, so that high-quality part finish can be achieved using vacuum casting process.
Secondly, the pattern is placed in a mould box and is filled with liquid silicone rubber.
Once the silicon gets cold, the mould is cut according to the split line established and the master pattern is also removed, which in result gives a perfectly formed cavity.
That mould cavity is then used to cast a large variety of epoxy or polyurethane materials. This way the manufacturing process produces high-quality parts in a short period of time.
The cost to create a silicone mould is much less than steel moulds; they can be manufactured very easily in 4-10 days; however, this also depends on the making method of master pattern and its complications. Each mould can be reused to manufacture 15-30 castings.
The manufacturing industry is recommended to use the mould with having wall thickness not less than 0.8mm and the recommended size is more than 1mm. Parts made from vacuum casting are not suitable to injection molded parts due to the difference between the conditions and manufacturing method. Using mould with thin wall sections are usually not recommended as the possibilities are there warping and cracking.
With the rapid development in the casting industry, we can get several benefits from vacuum casting. The working proficiency and delivering determinations are broadly improved and controlled. It is good to make full utilization of the focal points and be inventive to think of a few plans to better the pros and lower the cons. As such, vacuum casting demonstrates a brilliant future for casting industry.