Sheet Metal Fabrication refers to a
process of developing metal structures, a part of machine or a machine itself
from the sheets of raw metal. The process includes different methods such as
burning, cutting, shaping and welding the sheet metal to build a structure
according to desire. There are three methods that are used to convert sheet
metal into a product which are Hydraulic breaks, turrets/laser cutting and
welding. The process is done across the world but China runs some of the major industries of metal fabrication.
Types of metal and techniques of
fabrication vary in accordance to different types of project. Commercial,
industrial, structural metal fabrication use various metals in order to fulfill
the demand of their client, some of the commonly used metals are stainless
steel, aluminum, titanium, steel, copper, molybdenum, alloy and more.
Converting an idea of product into a
3D design is the beginning of sheet
metal fabrication process. In this stage, the client
shares his idea about the product with the designing team and both then work
together on the project in detail. Quality and quantity of metal are discussed,
after that the designers with the help of 3D design making software make a 3D
blueprint of the desired product. Now, the client is able to digitally view the
designs on computer.
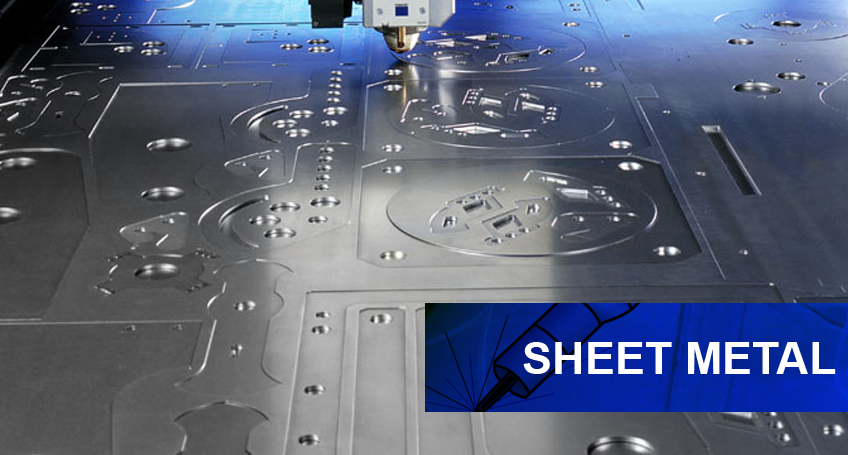
Once, the client approves the final design,
the development of product starts. A preliminary version is now created using sheet metal, stainless
steel or non ferrous metal as an actual sample of the product.
The most important and the lengthiest stage is
manufacturing phase. All the stages in manufacturing process require
differently skilled labor and tools. It starts with burning and cutting the raw
metal with cutting torches after that band saws and rolling machines are used
to form a desired shape. Shearing, hot and cold sawing, punching and bending
are some of the further processes in order create a structure out of it.
The final stage of the process includes
welding which is used to join the fabricated pieces to make the desired
product, warping is used to protect the product from defects. After all,
plating, powder coating and painting are done as the finishing process.
Once the product is ready, it goes further to
the quality check department, where the quality inspector checks the product
thoroughly to make sure the client gets the standard quality product without
any defects. After which the product goes to shipping department where some
packaging techniques are performed making sure the product will be shipped
completely safe and secured. We are a professional manufacturer of sheet metal
fabrication.